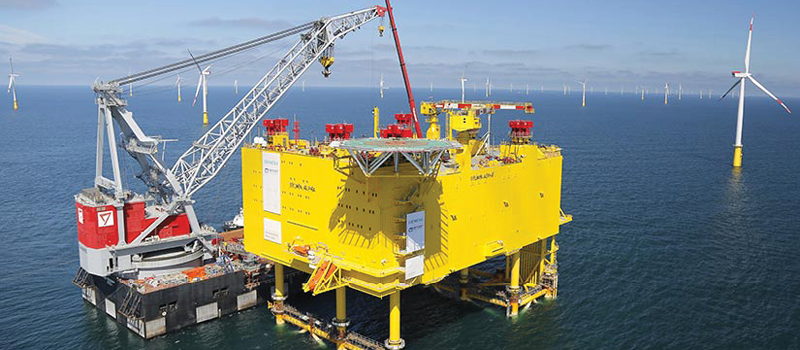
The general view of stainless steel is that it is a high-grade alloy that never rusts when in reality, it does. While stainless steel, in theory, should not corrode, there are many occasions where rust forms on a stainless steel product. This is especially true in marine environments.
In lower quality stainless steel or poorly made stainless steel products, it could be that the chromium levels are not high enough or evenly distributed. Stainless steel generally contains between 12-30 per cent of chromium, which protects it as long as the localised concentration is over 12 per cent.
The simplest condition for this rusting is when ordinary steel is rubbed off or comes in contact with a stainless steel surface. This causes the localised concentration of chromium to fall below 12 per cent. Hence the chromium oxide barrier fails and causes pitting corrosion, which will be explained below.
Depending on its crystalline structure, stainless steel falls into one of three main categories (as mentioned in our previous article found here):
– Martensitic Stainless Steel
This is one of the least common types of steel produced by manufacturers. It is characterised by its two primary grade types, 410 and 420. Martensitic stainless steel is known for its remarkable anti-corrosive properties. It includes blends of elements like Molybdenum, Nickel, Boron and even Titanium in some cases.
– Ferritic Stainless Steel
This stainless steel class comes in grades 430 and 434. These are magnetic steel variants with low densities of chromium and nickel in them. They can be used in various applications ranging from kitchenware to industrial equipment, making them the best suited for engineering situations.
– Austenitic Stainless Steel
The most commonly used type of stainless steel is the Austenitic, with designated grades 304, 316 and 317. Of these predominantly used grade types, 316 stainless steel is the second most common of the 300 series. They are non-magnetic and corrosion-resistant. This property is why they are used in industrial and domestic situations.
After differentiating the types of stainless steel, it is important to recognise different types of corrosion that affect stainless steel, which include:
General corrosion:
Where the entire stainless steel surface can be attacked uniformly when the passive film disappears from the surface without being able to reform, this corrosion occurs when the surface is exposed to reducing mediums.
Specific corrosions:
Two forms of corrosion (pitting and crevice corrosion) are typical of stainless steel.
Pitting corrosion
This corrosion occurs when the passive film is breached or damaged (chemical attack, mechanical damage, the presence of microstructure irregularities such as non-metallic inclusions caused by machining).
Crevice corrosion
This is another form of localised corrosion caused by extremely low oxygen levels in a crevice. This type of corrosion generally causes no issues unless the stainless steel is in a stagnant solution where chloride accumulates.
Bimetallic corrosion (Galvanic corrosion)
For Bimetallic corrosion to occur, three elements are required. Dissimilar metals, metal-to-metal contact, and metals in the same conduction solution (usually called an electrolyte). If any of these elements is missing, galvanic corrosion cannot occur.
Stress corrosion cracking
Tensile stresses in specific environmental conditions can lead to stress corrosion cracking.
General corrosion
This generally occurs when stainless steel has a pH value of less than 1.
Intergranular attack
When heating austenitic stainless steel at around 450 to 850 degrees celsius, the carbon within the steel converts to grain boundaries, leading to corrosion.
Choosing the correct corrosion-resistant grade of stainless steel
Before determining the appropriate grade of stainless steel for your project, you must acquire information about the contents’ temperature, pH level and chemical composition. Of those prerequisites, it is extremely important to ask how much chloride (salt) is present in its chemical composition.
Data reports often measure milligrams per litre (mg/L) or sometimes as parts per million (ppm) of Cl. But it is imperative not to confuse chloride with chlorine, as Cl is also the symbol used for the element chlorine.
In marine environments where stainless steel is exposed to salt water and sun for long periods, special types of stainless steel are usually required. The most appropriate stainless steel applications are designed using the following grades of stainless steel:
304L Stainless Steel
One of the most common grades for making components that will hold well when exposed to salt water but not submerged in it. It is an austenitic alloy that includes chromium and nickel and is lower in carbon than the standard 304 grade of stainless. Often used in water theme parks with salt water tanks and pools.
316L Stainless Steel
Also commonly used for marine environments, similarly to 304L with its lower carbon, an austenitic alloy containing chromium and nickel. Adding molybdenum provides an increased level of corrosion resistance than 304L and proves particularly useful in environments where salt water meets fresh water.
Duplex Stainless Steel
Duplex stainless steel combines ferritic and austenitic steels, resistant to pitting, stress corrosion cracking, and crevice attack. 2507 duplex stainless steel is a group of super duplex grades often used in the construction of offshore oil rigs and found in marine cranes for hauling boats in and out of salt water.
Although stainless steel has its drawbacks in a marine environment, it is still the most preferred material in the industry and offers the greatest underwater corrosion resistance.