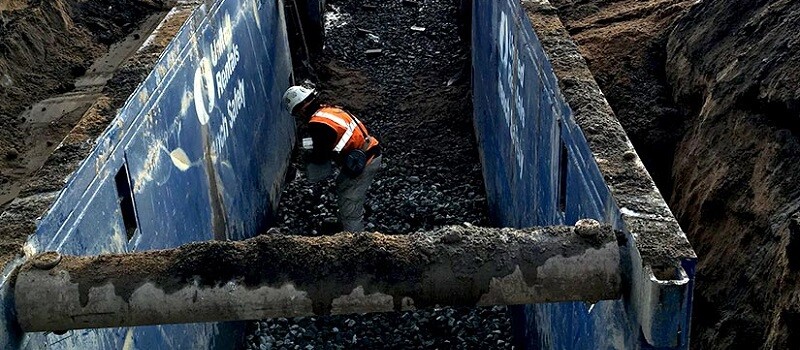
Stainless steel can perform exceptionally well buried underground for long periods. However, when in contact with moisture and aggressive chemicals such as chloride ions, sulphates and stray currents, it can cause localised corrosion. That is why buried stainless steel requires more consideration than above-ground stainless steel materials.
Buried steel pipelines typically begin to experience soil corrosion when it meets one or more of the following conditions:
- A pH value less than 4.5
- A resistivity less than 2000 Ω · cm
- High moisture content
- Presence of chlorides, sulphides and bacteria
- Presence of stray currents.
What are Factors Influencing the Performance of Buried Stainless Steel?
Soil pH Value
Apart from the salts such as sulphates and chlorides, the pH value of the soil in which the stainless steel is buried plays a major role in corrosion and degradation. More acidic soils may represent a serious risk to common construction materials, including some stainless steel grades.
Soil acidity is produced by mineral leaching, decomposition of acidic plants, industrial wastes, acid rain and certain forms of microbiological activity. If the pH level is kept great than 4.5, corrosion of buried stainless steel due to acidity is unlikely.
As a rule of thumb, well-drained soils are generally found to be less corrosive than poorly drained ones. Backfilling pipe ditches with sand provides reliable long-term protection in corrosive soils such as silt.
Soil Resistivity
Table 1. Soils classification based on physical properties, chemical composition, and resistivity
Type of Soil | Physical Properties (Particle size, plasticity, moisture, …) | Chemical Composition (Main constituents and contaminants) | Resistivity ( Ω . Cm) |
Sand | Particle sizes: Fine: 0.02 / 0.06 mm Medium: 0.06 / 0.02 mm Coarse: 0.2 / 0.6 mm Good Drainage | SiO₂, … | 10,000 to 500,000 |
Gravel | Particle sizes: Fine: 2 / 6 mm Medium: 6 / 20 mm Coarse: 20 / 60 mm Excellent Drainage | SiO₂, … | 20,000 to 400,000 |
Loam | Plastic mixture High moisture | SiO₂, Al₂O₃, … Dissolved species: H⁺, Cl⁻, SO₄²⁻, HCO⁻₃, … | 3,000 to 20,000 |
Clay | Very plastic mixture High moisture | SiO₂, Al₂O₃, … Dissolved species: H⁺, Cl⁻, SO₄²⁻, HCO⁻₃, … | 500 to 2,000 |
Silt | Coarse clay High moisture | SiO₂, Al₂O₃, … Dissolved species: H⁺, Cl⁻, SO₄²⁻, HCO⁻₃, … | 1,000 to 2,000 |
Corrosivity is directly linked to electrochemical reactions in soils. Soil resistivity usually lessens with the rise in moisture and the concentration of chemical species. Based on the table above, sandy soils have a high resistance to corrosion, with silt soils (coarse clay) being the most highly corrosive.
Table 2. Commonly used corrosivity index for soils according to resistivity.
Soil Parameter | Soil Corrosivity | |
1 | Soil Resistivity (ohm.cm) [28-30] | |
> 20,000 | Essentially Non-Corrosive | |
10,000 – 20,000 | Mildly Corrosive | |
5,000 – 10,000 | Moderately Corrosive | |
3,000 – 5,000 | Corrosive | |
1,000 – 3,000 | Highly Corrosive | |
< 1,000 | Extremely Corrosive | |
2 | Chloride Content (ppm) [28-30] | |
< 100 | Mildly Corrosive | |
3 | Sulfate Content (ppm) [28-30]; | |
< 200 | Mildly Corrosive |
The level of moisture contributes to the soil resistivity, which then determines the reciprocal of conductivity for a particular soil. A low resistivity indicates that soil will be a good electrolyte.
Stray Current Corrosion
Stray current corrosion refers to corrosion from the current flowing through paths other than the intended circuit. Also known as stray current electrolysis and electrolytic corrosion, the outside source forces the current through the cell, and corrosion occurs at the anode where the conventional current leaves the metal. As it is externally induced, it is independent of environmental factors such as oxygen concentration or pH.
A common source is direct current-driven trains or trams, which can cause severe damage to pipelines if the rails, the system’s intended current return path, are not completely insulated from the soil. If an underground pipe or other metallic equipment picks up a portion of this current, it will corrode at the point where the (conventional) current leaves to rejoin the original circuit.
Alternating current is generally not a cause of the corrosion, but in rare cases, a small portion of the AC may become rectified to direct current, which then causes corrosion.
Figure 1: Stray current due to an electric railway.
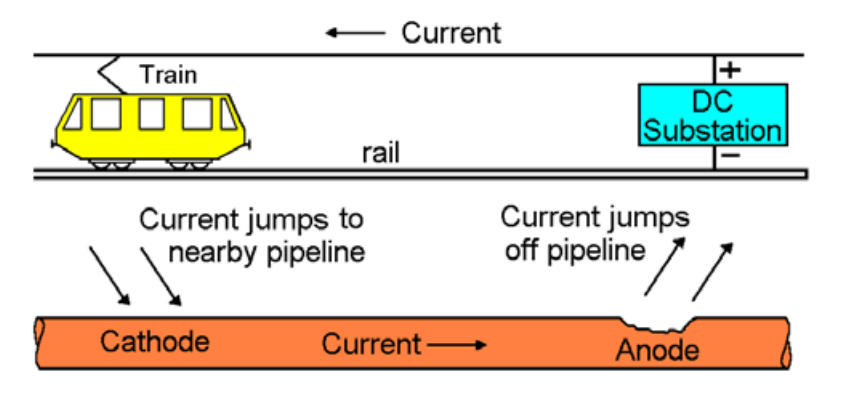
Presence of Aggressive Chemical Species
A common view with stainless steel underground is that one of the most important factors is the chloride ion (Cl) concentration in the soil and the soil moisture, which can contain different dissolved species such as sulphate ions.
Chloride contents are conducive to diminishing soil resistivity, thus providing a more favourable environment for corrosion. They may be found naturally in soils as a result of brackish groundwater and historical geological seabeds or from external sources such as chemicals applied to roadways. The chloride ion concentration in the corrosive soil electrolyte will vary as soil conditions alternate between wet and dry.
Sulphates are generally considered to be less reactive compared to the aggressivity of chloride ion levels. The presence of sulphates may pose a risk as sulphates can be converted to highly corrosive sulphides by anaerobic sulphate-reducing bacteria.
Microbiologically Influenced Corrosion (MIC)
There are many types of bacteria known to cause microbiologically influenced corrosion of stainless steel in common soil conditions. These bacteria can be broadly classified as:
Aerobic: – This requires oxygen to become active,
or
Anaerobic: – Where oxygen is toxic to the bacteria.
Sulphate-reducing bacteria (SRB) is anaerobic and is the cause of most instances of accelerated corrosion damage to ships and offshore steel structures. Iron and manganese oxidising bacteria are aerobic and are frequently associated with accelerated pitting attacks on stainless steel at welds.
How do you Enhance the Reliability of Buried Stainless Steel?
Despite the substantial additional risks, there are steps one can take to ensure the buried steel gives the longest service underground.
Selecting the Appropriate Type of Stainless Steel
Where a structure is situated both below and above ground, undertake one of the following:
- Decide on a common grade of stainless steel for the entire structure. Choose a material that will provide the required asset life in both environments.
or
- Decide on different materials for the below-ground and above-ground environments. The transition from one to the other at approximately 500mm above the finished surface level. Where different metals are to be joined, ensure that dissimilar metal corrosion risks are adequately controlled by insulating one metal from the other.
The three commonly used types of stainless steel are:
Austenitic Stainless Steel
This category comprises grades that are highly resistant to corrosion. It covers 304, 316 and 317. Grades 304 and 316 are widely used in equipment and piping to handle freshwater. Observing these guidelines can prevent crevice and pitting corrosion. (For more information on the corrosion resistance of stainless steel, click here.)
Duplex Stainless Steel
Duplex Stainless Steel is a combination of ferritic and austenitic steels, resistant to pitting, stress corrosion cracking, and crevice attack. The presence of chromium, molybdenum and nickel makes Duplex Stainless Steel super resistant to carrion. Molybdenum, in particular, has been found to enhance the stability of the passive film, thereby minimising localised corrosion.
Super Duplex Stainless Steel
Compared to Duplex Stainless Steel, this category of stainless steel has much higher levels of molybdenum and chromium content. This, in turn, gives Super Duplex Stainless Steel a higher resistance to acid and chloride corrosion.
Table 3: Minimum Requirements for Stainless Steel in Buried Applications
Asset Type | Min SS Grade Required |
Low-risk SS component (1) | 316 |
High-risk SS component (with soil monitoring) (3) | As per Table 4 |
High-risk SS component (no soil monitoring – further than 2km from a coastline or maintenance item) | 2205 or petrolatum tape system wrapped or coated 316 (4) |
High-risk SS component (no soil monitoring – within 2km of a coastline)- maintenance items excluded | Super duplex or petrolatum tape system wrapped or coated 2205 (4) |
Table 3 Notes:
- Low-risk Stainless Steel components are those that have fully automatic redundancy or a contingency that can be rapidly implemented. Typically, this includes water reticulation items.
- High risks are all other assets. Typically, this includes all pressurised sewerage items and distribution water main items.
- Soil analysis shall be undertaken to determine the chloride ion concentration, pH and soil resistivity so that Table 4 can be applied to select grade. Soil measurements shall be taken at each location where stainless steel-containing assets are to be located or every 100m where continuous stainless steel-containing assets are to be buried underground. Where several measurements yield the same result, and the ground conditions are clearly consistent, testing levels may be reduced.
- Refer to Clause 15.20 of the MRWA edition of the WSAA Water Supply Code WSA 03—2011-3.1 and MRWA-W-306A for petrolatum tape system application details.
Table 4: Preferred Minimum Grades for Buried Stainless Steel Applications:
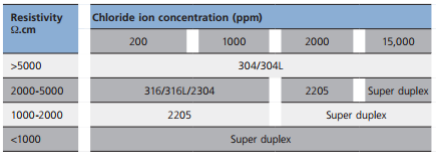
Properly Fabricated Stainless Steel
Regardless of the structure, there are many things to be considered during fabrication. Oversights in the processes can compromise the quality of construct. One of the common fabrication problems is embedded iron particles and filings that later initiate corrosion on buried steel structures. Other surface contaminants such as common salts, carbon steel, dust and grime also compromise the quality of the stainless-steel output.
Take welded stainless steel tube as an example. During pickling, an electrochemical process of removing contaminants, steel is heated by welding. Because of process malpractices, the damaged metal layer on the steel surface may not be completely removed, thereby sending to market stainless steel that is prone to corrosion. Of course, this risk can be easily and entirely eliminated by using a press fit system.
Proper Installation of Piping and Other Stainless Steel Structures
Clean or fine sand is the preferred soil for burying pipelines, cables, and other stainless installations because of its higher resistivity. Backfilling must be done in a way that aeration is always maintained. When soils are compacted, drainage and aeration problems result, thus creating an enabling environment for corrosion.
Other than backfilling and compaction, organic materials must be avoided and should never be included as part of the fill. Such matter attracts microbial activity, which, if intensified, can corrode stainless steel surfaces.
Prior to burying the steel pipe, consider wrapping it in protective tape or bituminous coating to prevent external corrosion.
General Conclusion
The long-term effective use of stainless steel underground will depend on soil conditions, steel grade type and even fabrication practices of the stainless steel piping. Once installed properly, stainless steel can provide exceptional service underground, making it the go-to option for its resilience over plastics and copper and its corrosion resistance over carbon or galvanised steel.
Bibliography
- Guidelines for the use of Stainless Steel Underground. Australian Stainless Steel Development Association (ASSDA), Australia [Accessed 26 August 2019].
- Cunat, P. (2001). Corrosion Resistance of Stainless Steels in Soils and in Concrete. World Stainless, Brussels [Accessed 26 August 2019].
- Different Types of Corrosion. WebCore Corrosion Consulting Services, Singapore. [Accessed 26 August 2019].
- Stainless Steel Specification AM2762. South East Water, Australia. [Accessed 26 August 2019].
To speak to one of our experts about using stainless steel in your project. Contact us today!