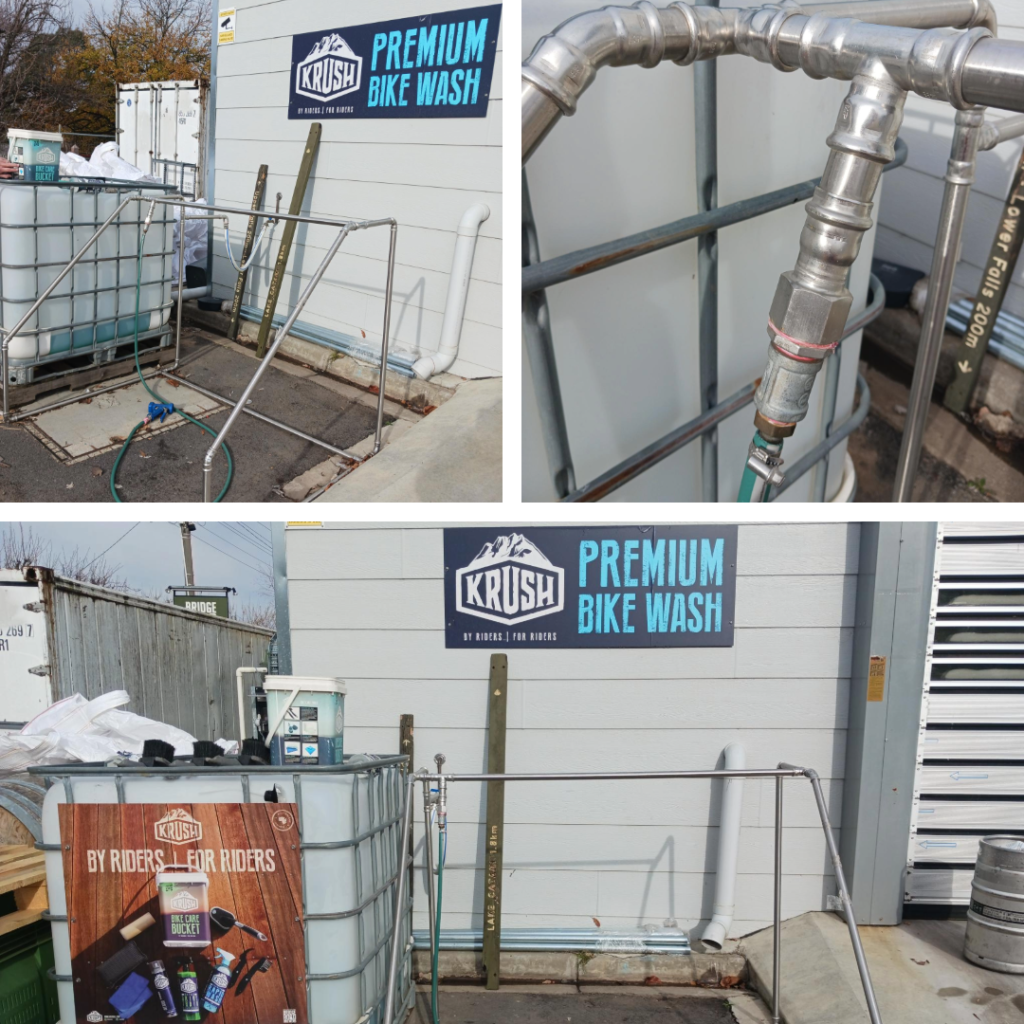
Introduction
Bridge Road Brewers (BRB) have a long history of supporting cycling, both in their hometown of Beechworth, but also nationally through partnerships with multiple grassroots clubs and events.
This history allowed a relationship with Krush bike wash to be formed, with Krush providing their products for free to allow BRB to create a much-needed resource in Beechworth: a bike washing station.
Beechworth has a significant amount of mountain biking infrastructure, including the newly established Indigo Epic trail. However, the town was missing a public location for people to wash down their mountain bikes post ride.
Background
The idea of the station was to create a universal bike stand or rack to hold any bike for washing, whilst ensuring full access to all parts of the bike, particularly the drive train, ensuring this remained clear from the ground with the freedom to be rotated.
BRB had previously used Ibex Australia’s Impress stainless steel press fit range in the brewery on a recent expansion and efficiency project, specifically in capturing excess potable hot water from the brewing process.
On a tight budget, Ibex Australia’s stainless steel press fittings allowed the brewery team to undertake the project themselves, without the need for purge welding skills. The fact that the tools required to cut, and press were also available for rent through their local retailer, Reece, made the project cost effective and fairly straight forward.
BRB ended up having some pipe lengths and a few odd bends left over for this project and the team saw the opportunity to create something unique for the town’s bike wash station.
Solution & Results:
Bridge Road Brewers used Ibex Australia’s range of Impress 316L Stainless Steel press fit tees and elbows to create a functional frame that not only held the bikes, but also carried the water to wash them. The bike stand frame itself is the water piping, with the added weight of the water within the frame providing stability to the structure. The strength and consistency of the fittings allowed for straight forward construction, where BRB only had to worry about accurate pipe lengths. The pressing of the fittings ensured the structural strength based on some simple design drawings. The ability to press all fittings after roughing together as the final step really enables confidence and in turn a fast solution.
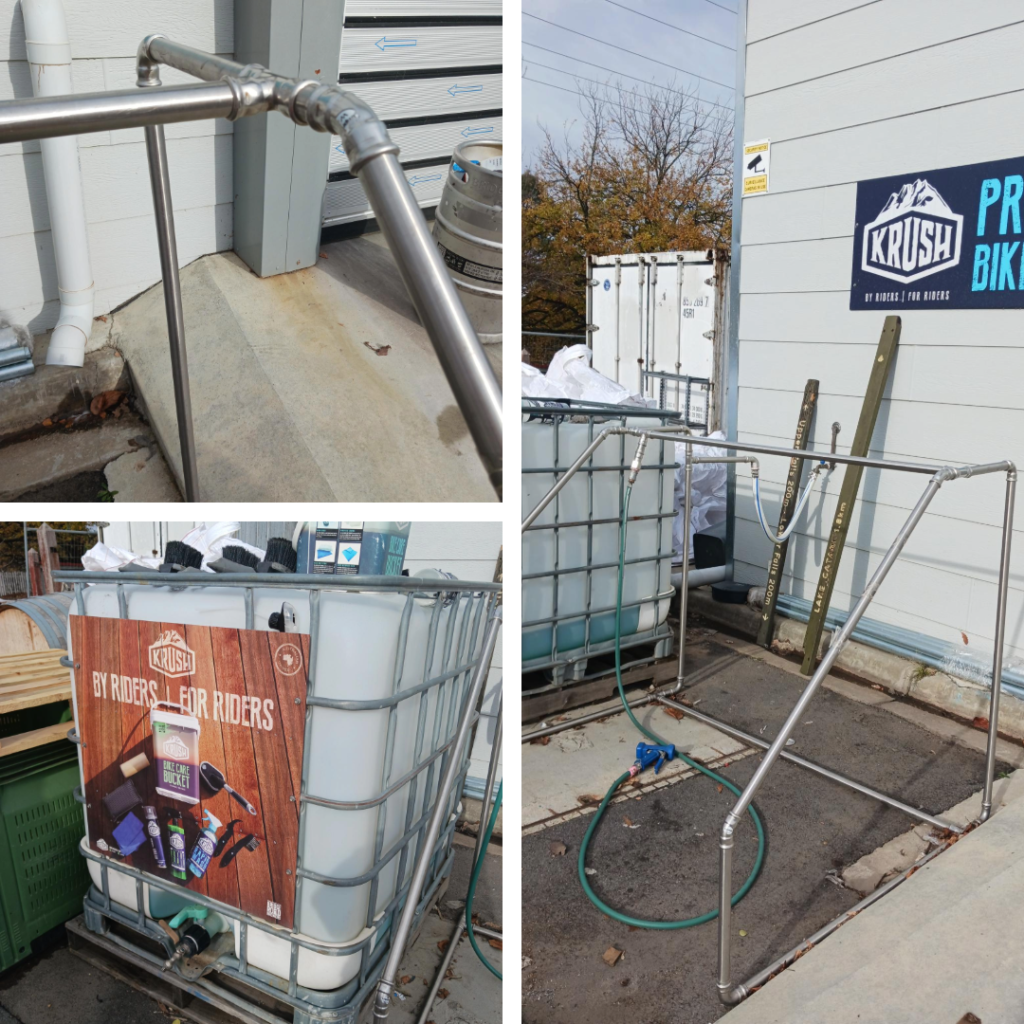